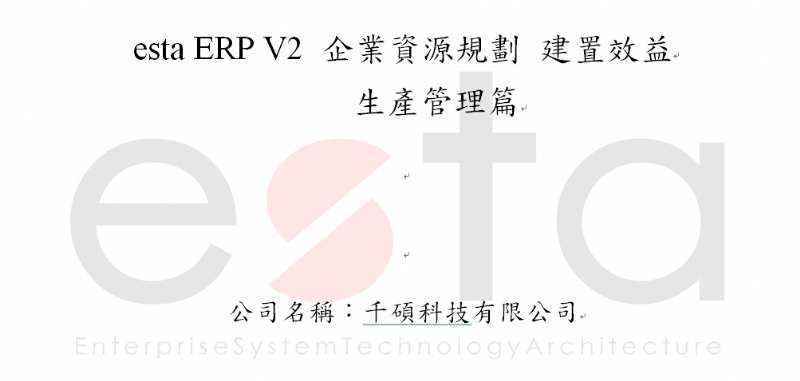
ERP 企業資源規劃 建置效益 -生產管理篇
<<節錄 >>
二. ERP系統建置與實施
6. 生產管理的核心作業 –MPS與MRP
MPS主生產排程的主要任務是讓ERP的生產管理模組能夠支援業務銷售計劃,達成ATP(Available To Promise)及CTP(Capable To Promise)的目標,亦即讓生產計劃能配合接單、銷售計劃。
MPS以BOP + BOM為生管基礎(上個世紀早期的發展只有BOM的基礎架構,並無BOP的模式),接收PP生產計劃的製品數量與需求日期,並以RCP粗略產能規劃(關鍵產能限制)來確認生產排程是否可行。而MPS要能夠做到ATP與CTP,必須由MRP來確定原物料供應能否支援ATP,而CTP則是交由RCP來確認產能是否超過限制。
MPS是連結業務銷售與生產管理的接口(Gate)、整合生產的規劃(Plan)與控制(Control)的關鍵模組,聯繫長期巨觀(Macro)生產計劃與短期微觀(Micro)製造執行的功能,MRP規劃的需求依據是來自於MPS的產出資訊。
生產批量與需求/供應時段也是MPS的重要考量參數,生產批量是生產能力與資源供給的最佳經濟規模衡量(與製造工廠設備規劃及資源配置相關),需求/供應時段則是最佳的作業與管理週期考量(通常以週為單位),這些考量與時間區間DTF有重要的關連,1970年代以前工業產品多樣化及市場需求快速變化的情形還不常見,JIT(Just In Time)與消除浪費的生產觀念也尚未從日本傳播出來,考量需求/計劃區間內的需求時段與經濟生產規模批量乃是MPS的主要功能。
而傳統的MRP物料需求計劃(Material Requirement Planning)及後續的MRPII (Manufacturing Resource Planning)是1960~1980年代由Joseph A. Orlicky、Oliver Wight等學者逐步建構出來的(實務上則是由BOSCH、CASE等公司在生產管理電腦化上實現出來)。1960年代商用電腦剛剛萌芽,在資料處理與數據運算能力相當有限的情況下,傳統MRP以較長的時間區間(通常以週為單位),計算來自於市場銷售需求及生產製造物料表BOM組成所需的數量、時程。
90年代以後,隨著IT產業軟硬體技術進步,及全球化各種管理觀念的進化與傳播(e.g.日本製造及TPS、JIT等),傳統MRP的模式與方法已經無法應付目前複雜多變且快速的製造環境與生產供應鏈的管理需求,特別是電腦計算能力與資料儲存容量的大幅增長,推動了MRP技術的進化。
esta ERP V2具備3種MRP模式 :
❶ MRP-for JIT 也可稱為MRP-for LEAN(精實模式),這並非傳統MRP所具備的功能模式,而是因應精實生產模式及TPS模式而進化的MRP功能,它依據BOM物料(子件)投料製程設定,由BOP提供製品製程作業的基礎參數,讓MPS排程計算所需物料數量及時程,達成Just In Time的精確數量、時程的控管,杜絕物料供應不準時所帶來的製程產能閒置或是存貨堆積的浪費。針對每一筆需求(e.g.工單領料…),規劃該取用庫存亦或是必須請採購。同一筆需求可以部分數量取用庫存,不足的數量請採購供應。MRP-for JIT模式可達到將物料之庫存水位降至最低的效益,理想目標是達成零庫存(需要整個供應鏈的配合與管控制度)。適用於需求明確且高成本、較重要或體積過大之原物料、零組件。是企業實現TPS或是LPS的Just In Time及時供補系統的MRP模式。
(未完) ................................................................................................................................
...........................................................................................................................................
若需要完整 {esta ERP V2 企業資源規劃 建置效益 -生產管理篇}文檔, 請在 本網站訪客留言 , 並請註明 索取者 / 公司(單位) / 使用目的 / Mail Address. (文檔將會以 e-mail 方式傳送)
J.L. March Lee (引述本文內容, 請以本網站訪客留言,取得作者同意)